
I still get asked to fettle cars and scooters now and again, I still have all my tools but mechanical work is cheap here so most people get things done in town. There is always work to do when you own a boat and I own 4 so there is always work to do. Winter is the busiest time of course because the boats are out of the water and all the ideas that have sprung to mind during the summer, to make them better, can be tackled. They also need to be looked after. Three of my boats are wooden (plywood and fibreglass) and they'll start to look tatty after a busy summer so they get a going over.
I also like making model boats and I currently have 4 on the go. The best thing about the models is that you can put them down for a while and come back to them when there's more time for hobbies. So, I thought I'd document some of the bits and pieces that I do so that you can see that ex-pat life isn't all beer and swimming pools.

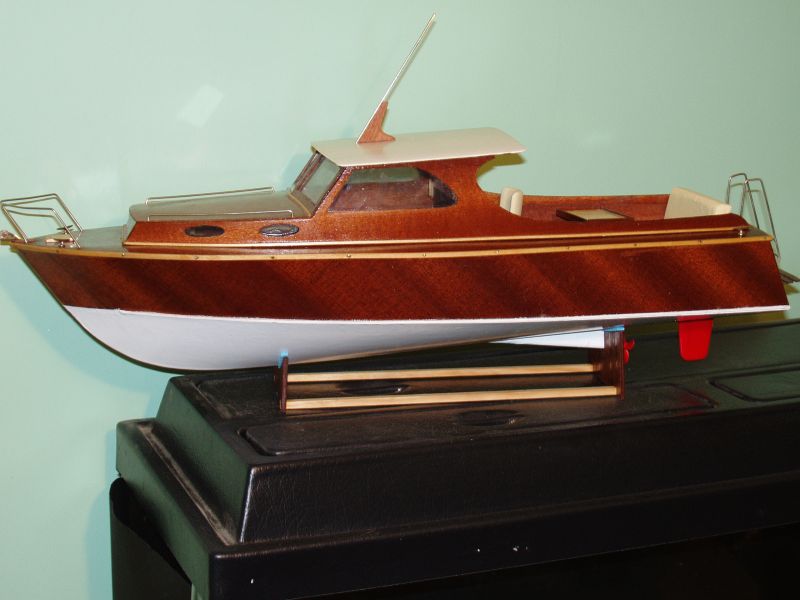
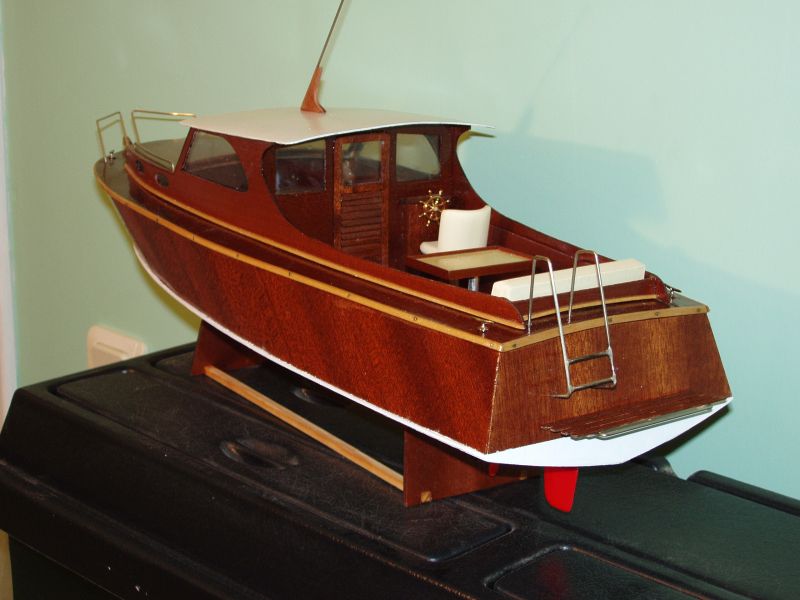
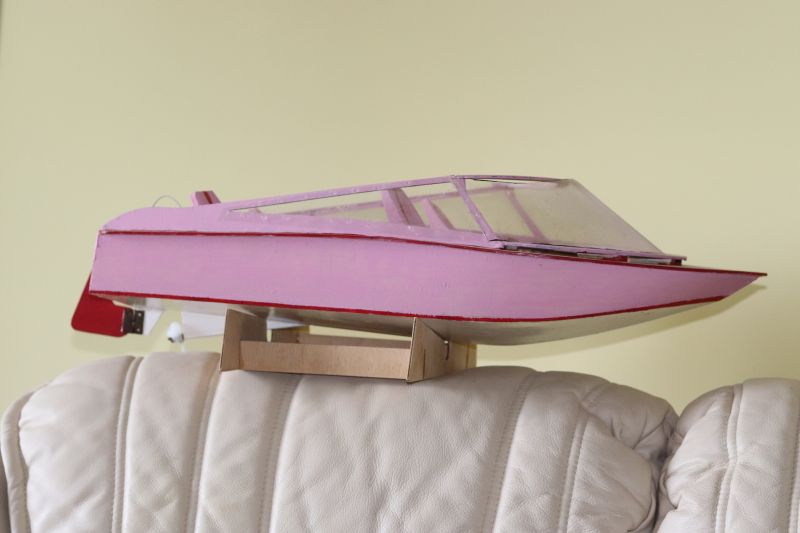
The pink boat is scaled to fit a Barbie doll and my grandaughter usually brings 3 or 4 of them with her when the family come on holiday and gives them trips round the pool.
Current projects are some work on my big boat (although I'm under house arrest so I can't get up to where it's standing to do what I need to do), making new kitchen cupboards and a hard roof over the back end; a bit of re-furb work on the trimaran and 2 RC model boats for friends. I've been making bulkheads for those today and will make some more tomorrow when I'll start taking some pictures. I also sanded the rear aka off the trimaran today and I will probably start on the front one tomorrow. Again, I'll get the camera out for that.